日报标题:「别逗我,车灯不就是给灯泡加个塑料壳子嘛」
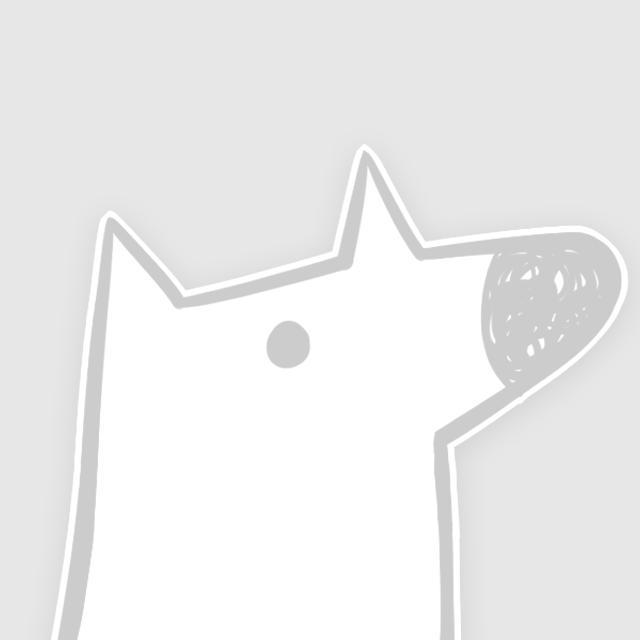
所有塑料内外装饰件,诸如车灯,前后保险杠,仪表板,中控面板等等。这个得慢慢说了,先占坑。
1. 车灯
我们日常所见的车灯,大家可能只关注的是是不是 LED 大灯,矩阵式 LED 大灯这些抽象的名词,但是其背后却是非常多学科技术的集合结晶。先不说昂贵的光学组件,牛逼闪闪的光导这些光学器件,就是单单承载这些的壳体,进行反光的光学面结构,透明的灯罩这些,就非常难搞。首先大灯光电转换的效率比较低,很大一部分电能都转换为热能散失了,所以前大灯设计了各种的散热设备,这些很多都要集成安装在灯壳上,往往安装的方向又和灯壳的出模方向是不一致的,这又要用滑块或者斜顶成型,所以不仅仅自身产品结构复杂,而且模具也非常复杂。加上随着车灯技术的发展,各种绚丽的灯带,光导,激光大灯这些技术的应用,使得前大灯的壳体设计越来越复杂。而我们普通消费者,只可能认识到这是一个塑料壳子,但是却不知道车灯工程狗在开发阶段被这灯壳子虐得是体无完肤啊。
再说灯里面的那些反光光学面,就是我们日常尾灯里面常见的那些方块面。
这些面不是我们随便开脑洞画出来的,这是我们光学工程师经过计算,然后用专用的工具做出来,输入给产品设计狗,一片一片抠出来的。你以为我在软件里把面抠出来就完了吗?Too Young!这是注塑件啊,你是不是得考虑一下材料收缩率,就按 0.5% 算吧,算了一下,你告诉了光学工程师,你给我这个镜面在产品上做出来会有一点点偏差。光学工程师怒了,卧槽,你玩我,不行,要是光束射出来有偏差你们是要负责的!怎么办,你没办法,模具上想办法吧,放一点收缩率。你以为万事大吉,开心的放了国庆假和女票双宿双飞,不亦乐乎。回来一看光学工程师一脸你他妈逗我的表情。
原来是你抠的面注塑出来有缩印,反射出来的逛畸变了,本来是射地的,现在改射天了。你吓一大跳,卧槽,怎么回事,怎么回事,一检查发现有一处厚度不均匀,导致此处有缩印。你顿时觉得,一世英名,毁于一旦,都贵自己想着和女票度假,检查不仔细。改吧,你无奈的说,拿起你的剪刀,不对,你软件里的剪切修改工具,开始缝缝补补,不一会儿就弄好了,光学工程师表示很满意,你长松了一口气说,做了点小贡献。(非车灯行业,纯属脑补)
如果我们去看这些光学面的剖面,从大的尺度上,此处壁厚基本均匀,放大之后,再内壁上就能发现细小的凸包,这些就是光学面。
灯罩不详细说,可以想象,不仅仅是外观件,而且还是因为其要投射车灯灯光,对产品的质量要求更加严格,设计需要把控的自然也不简单。
2.保险杠
普通消费者对保险杠的认知,可能还停留在这就是一块塑料壳。对,我们就是这么任性,车上全是塑料壳。对于设计人员,一个前保险杠,可能是最复杂的外饰件之一了。首先是,周边环境复杂,对口件太多。引擎盖啊,挡泥板啊,轮胎包络啊,各种灯啊,水箱位置啊,防撞梁啊,脱钩啊,雷达啊,AEB 啊等等。
作为一个产品设计汪,你真在专心致志地做数据,开闭件工程师跑过来,你这里这里圆角倒得有问题,导致视觉间隙很大,得改一下。你一看这么大一个锅,也不敢独自背啊,卧槽,这圆角特么是 A 面上的圆角,我能改么,你找 Style 吧(造型设计师打了个喷嚏)。开闭件工程师一看,吆喝,放大招啊,好啊,找造型去。这边刚走,轮胎工程师又来了,刚才把轮胎包络重新做了一下,变大一点,你这里这里的卡扣和紧固点距离包络的间隙不够安全值,都得改……你一听把刚和的水全吐轮胎工程师脸上了,大哥,不带这么玩的,你知道工作量有多大吗?轮胎工程师表示没办法,专家给的新算法,更精确。这个好像没法推了,怎么办,我水还没喝完呢。你把轮胎包络先发给我吧,我看看。已经发给你了,你查查邮箱,你滚!这边轮胎工程师刚走,冷却系统的工程师又来了,你预感到一层黑暗气息轮罩了你的办公桌三尺范围之内。忙哈,我刚才又算了一下进风面积,你这里这里做的结构把进风口挡住了,不利于水箱散热,格栅这里需要做一下调整……此刻你脑子里只有调整调整两个字在循环,心里想着特么你两个字我 B 面结构就要重新做了。正在这时,电器工程师跑过来拍了一下你的肩膀,露出迷之微笑,上面决定了,高配车型要加装 AEB 系统,格栅这里这里结构需要更改,还有增加一个低配时装饰用的装饰盖。唉,你怎么打人啊,打人是不对,啊啊啊啊……大家都走了,你又开始一个人忙碌,把工程更改梳理梳理吧,一晃太阳西斜,快下班了,你的心情顿时明亮了起来。你站起来伸了伸腰,活动活动筋骨。这时,电脑右下角传来一声 Outlook 魔性的邮件提醒声,你大叫一声不好,然而为时已晚。来自造型设计师的邮件,就五个字:
面用原来的
你,卒。
你以为完了,可以神游天国了,怎么可能,CAE 工程师救活了你。您还不能走啊,分析结果显示,你这里的结构太硬了,不利于行人保护;然后你这里的结构又太软了,不利于低速碰撞。你先把这两个问题解决了再走吧。你下班了,但是明天还得继续战斗。这就是一个保险杠产品工程师的日常。
保险杠从外观上看,没什么,确实是一个塑料壳子,但是其 B 面结构的设计非常复杂,各种对手件的集成设计,还有法规项的考量,卡扣形式的选择,都是需要慢慢去抠接口,做布置,挑战其他系统,也对其他系统做出各种妥协的结果。除了这些之外,考虑模具的影响,浇口的布置,各种接口的实现,又得对现有结构进行优化。考虑涂装的影响,又要根据工厂的涂装线规划,机器人的能力,对产品做出修改。装配线,运输悬链等等,都会对产品的设计产生影响,设计一点都不简单。
3. 仪表板
和保险杠一样,因为布置在其上的接口多,各种按键,仪表,电器件等等,接口设计极其复杂。为了追求良好的触摸质感,制造工艺复杂,搪塑啊,吸塑啊,发泡啊,都会给设计带来困难。储物盒的布置,你得放的小各种东西吧,你还得考虑人机工程,大部分人能伸手够得着吧。仪表的事业不能遮挡,还得遮光放炫目,以免驾驶员看不清仪表上的指针数字。仪表板还不能太高吧,以免遮挡驾驶员的视野。和门护板,玻璃,中控的间隙你得控制吧,不然不美观。车内 VOC 得考虑吧,你看对门奔驰都因为这个被诟病,我们三线小自主,得学着点啊,材料不能乱用,选个味道好点的。
以仪表板副驾驶布置副驾驶气囊那个区域,算是仪表板上难设计的一个典型。大家都知道,气囊是布置在仪表板下面的,所以当遇到碰撞事故时,气囊在加速度的作用下经过传感器引爆,把这个区域的仪表板炸裂,然后气囊充气鼓起,对乘员形成保护。所以,这个区域的仪表板厚度需要精确控制,厚了不行,炸不开啊。所以这个区域一般会做弱化减薄处理,有些做到零点几毫米。但是做薄呢,又回带来外观问题。为什么呢,PP 材料对厚度变化特别敏感,这个区域厚度的突变,往往会产生比较明显的缩影,而仪表板一般是要腐蚀皮纹的,皮纹对于缩影这种缺陷是起放大作用的,所以会非常明显。
还没完,产品出来了进行气囊爆破试验,炸裂的仪表板碎片,也要控制,不能太大,重量要控制,以免爆炸后飞出伤及乘员。如果不合格怎么办,回来改结构,再分析,再试验,到合格为止。